FOCUS ON GLOBALIZATIONA Shift in Engineering Offshoring
The transfer of R&D resources to low-wave countries may portend major changes for engineers in developed nations.
By Alan S. Brown
Companies have been offshoring manufacturing for decades. Today, however, corporations are sending engineering work abroad as well, by outsourcing work to offshore vendors or assigning it to overseas divisions.
If this is a seismic change in the engineering profession, so far mechanical engineers have only felt the initial tremors. The trend is most pronounced in information technology, computing, and consumer electronics, where U.S., European, and Japanese firms have hired hundreds of thousands of programmers and engineers in China, India, and other developing nations. Computer and cellphone manufacturers increasingly outsource product design and engineering to original design manufacturers in China and Taiwan.
Many IT organizations not only outsource projects overseas, but rely on a small army of contract workers from overseas (on H1-B visas) to staff U.S. offices. Some companies require domestic IT employees to train their replacements (who will return overseas with their jobs) in order to retain severance benefits. A recent survey of 10,000 workers by the Stern and Wharton business schools found 8 percent of IT workers fired or involuntarily transferred due to offshoring.
Similar practices are not as common in mechanical engineering. Yet the trends are moving in the same direction. Companies like Caterpillar, Daimler, General Electric, General Motors, Honeywell, Siemens, Matsushita Electric, and IB
M have all built massive engineering facilities offshore. Many companies also outsource engineering to offshore vendors. [Photo: Manufacturing profits helped build Shanghai's skyline. Studies show companies that offshore manufacturing tend to offshore engineering too].
Corporations justify offshoring easily. They need local engineers to enter developing markets. They claim they cannot find enough skilled engineers at home. They want to speed up product introductions. They believe offshoring cuts costs.
There are other reasons too, some rarely enunciated. Many CEOs of public companies feel pressure from Wall Street analysts to show cost-cutting offshoring strategies. China demands technology transfer in exchange for access to its markets. Engineering must follow manufacturing abroad to achieve real efficiencies. Managers can hire four or five engineers overseas for the cost of one at home.
Offshoring is reaching critical mass in many engineering fields. Offshore engineers are bright, highly motivated, and have climbed the skill ladder rapidly. Engineering centers founded to create 3-D CAD files and adapt products for local markets are now tackling more complex projects as well as true research. Increasingly, large corporations see overseas divisions as new centers of excellence, and offshore vendors as low-cost sources of design and engineering.
This may sound familiar. After all, multinationals increasingly promote talented individuals from all over the world. Many have outsourced engineering projects for decades.
Yet many researchers believe offshoring today differs from past practices in one very important way: Many multinationals are making massive investments overseas at the expense of investments at home. This massive transfer of knowledge and capabilities overseas is depleting engineering capacity in developed nations.
This raises fundamental questions: Are multinationals transferring too much technology to potential competitors? Will fledgling engineers in developed countries become leaders if the jobs where they learn technical leadership skills are offshore? Can multinationals remain close to customersСand control project design and specificationСif they outsource vital engineering capabilities?
Multinational companies often answer questions like these by affirming that offshoring enables them to reduce costs to consumers, increase market share, and use profits to create more high-paying jobs. They are, after all, not citizens of one country, but of many countries, and their job is to maximize shareholder value.
ELUSIVE NUMBERS
European and Japanese engineers tend to have more job protection than American engineers, and U.S. corporations are believed to be in the forefront of offshoring. But there is little hard data on engineering. In 2005, the National Academy of Engineering asked Timothy Sturgeon, a research Fellow at MIT’s Industrial Performance Center, to assess data on offshoring.
“I documented something everyone already knew. There isn’t any data on any of this stuff,” he said. “I was shocked to find how big the holes were. The U.S. Bureau of Economic Analysis collects data on 16,000 product categories versus 17 service categories. I can find a synthetic thread twisted left, but all engineering is lumped under ‘Business, professional, and technical services.’”
Lori Kletzer, an economist at University of California, Santa Cruz, agrees. “It’s almost to the point of being ridiculous,” Kletzer said. “We’ve been a service economy for a long time, but we’re still focused on things that cross a border and require a customs form.”
In a recent study, two Rand Corp. researchers, James Hosek and Titus Galama, argued that the United States still leads the world in science and technology, accounting for 40 percent of global R&D spending. Compared with other industrialized nations, it filed 38 percent of all new patents, employed 37 percent of all researchers, and wrote 63 percent of the most highly cited research papers.
Yet Hosek and Galama cannot determine where U.S. corporations spend their R&D dollars, which amount to two-thirds of all U.S. R&D funding. 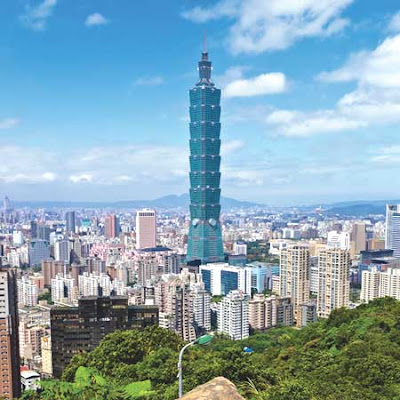
[Photo: Taiwan manufactures 90 percent of the world's laptop computers and does an increasing amount of design and engineering].
Often, information comes in illuminating bursts. A recent National Academy of Engineering report noted that employment and exports of Indian software services firms grew 30 to 40 percent annually over the past decade. And 18 of the top 20 U.S. semiconductor companies have built design centers in India, half since 2004.
Ron Hira, an assistant professor of public policy at Rochester Institute of Technology, notes that IBM’s Indian operations grew to 73,000 employees by the end of 2007, from 9,000 in 2003. IBM expects to reach 100,000 workers, mostly technical, by 2010. “That rivals the roughly 120,000 people IBM employs in the U.S.,” he noted.
Hira points to a 2007 survey of 248 American and European R&D managers undertaken for the National Academies’ Government University Industry Research Roundtable. The managers expected R&D employment to grow in India and China. More thought it would decline than grow in the United States. Most managers said they planned to keep emerging technologies at home while offshoring familiar science.
To understand offshoring better, Leonard Lynn, a professor of management policy at Case Western Reserve University, and Hal Salzman of the Urban Institute, a Washington think tank, turned detective. They interviewed more than 200 engineers and managers at 41 multinational companies and eight smaller firms at 67 sites in 14 countries. They covered 23 electrical or electronics sites, 20 auto or aerospace facilities, 19 information technology offices, and five medical or pharmaceutical centers.
“Based on our case studies, we are concerned about U.S. firms taking their market leadership for granted while undercutting their engineering infrastructure,” Lynn said.
Lynn is skeptical of many offshoring practices and assumptions. He said that, in once case, a multinational company’s division specializing in large administrative software systems announced plans to develop new software. When financial analysts criticized it for not having a cost-cutting offshoring strategy, senior management decided to outsource a percentage of the business. “It was not so much a strategy as a quota,” Lynn said.
The company, which Lynn calls ALL-IT to protect its identity, began outsourcing more of the project while downsizing U.S. staff. It had planned to keep core development in the United States. Yet as technical hurdles arose, the company no longer had the U.S. programmers to tackle them. It had to send more work overseas. By 2006, the company’s U.S. programmers were maintaining legacy systems while its Indian center was creating next-generation software.
The company, a systems integrator, remained close to its customers. Yet it often brought in staff from Indian contractors to help solve customer problems. “It was becoming apparent to customers where the real expertise lies,” Lynn said. ALL-IT’s managers told Lynn that they learned systems integration by moving up the ranks, but those jobs were being outsourced.
According to Lynn, “If you neglect the infrastructure back home, you lose capabilities. If you don’t have managers who worked their way through the entire system, then offshore engineers have to take over more leadership roles.”
Lynn and Salzman also studied a heavy electrical equipment manufacturer and a power systems company, which did a better job of safeguarding core technology. Both companies tapped Chinese or Indian nationals in top engineering management to lead their ventures overseas. The facilities started with limited agendas, like supporting a local factory or doing enough research to justify Chinese government contracts. Over time, though, their performance and the relationship of their managers with executives at home enabled them to expand their operations.
VALUE CHAINS
For many companies, offshoring engineering is an extension of outsourcing, a business model that calls for companies to concentrate on core businesses and contract peripheral projects to vendors. Companies that have prospered under this model often control the point where value is added to a product, often through engineering.
Take, for example, Apple. Its ability to develop proprietary technologies makes it a winner, said Kenneth Kraemer, the former director of the Center for Research on Information Technology and Organizations at the University of California, Irvine. He estimates that Apple captures approximately 30 to 35 percent of the value of each iPod it sells. Its U.S. and Japanese vendors, which supply high-tech components, receive most of the rest. China, which assembles the iPod, earns less than 5 percent.
Kraemer estimates that the iPod created 40,000 jobs. Only 12,000 to 14,000 jobs are in the United States, roughly half in engineering or management. Yet U.S. workers earn 2.5 times more than non-U.S. workers. “In Asia, the jobs are mostly very low cost labor, with relatively few engineering and management positions,” Kraemer said.
Even in a commodity business like PCs, some companies have proprietary advantages. Intel, which makes processors, and Microsoft, which develops operating systems, profit more than the PC makers themselves, Kraemer said. Hewlett-Packard and Dell have dominated the notebook computer market by leveraging the value chain, MIT’s Sturgeon added. This is true even though Taiwanese companies make more than 90 percent of the world’s notebooks and do an increasing amount of design and detailed engineering. “One Taiwanese executive once told me that no foreign PC maker ever kept its market share in the United States,” said Sturgeon.
This is because Dell and HP are strong marketers and use their position atop the value chain to cut costs aggressively. In notebooks, Sturgeon said, Microsoft and Intel standards determine most of the functionality. “That makes capabilities generic and parts substitutable, so HP and Dell can play one component manufacturer off against the other,” he explained.
Automakers tried to do the same thing, but with less success. Each automotive subsystem requires extensive customization. “This makes it very difficult for automakers to specify what they want suppliers to do,” Sturgeon explained. “They have to trade tacitСuncodified, mushy, analogСinformation. They sit around conference tables, look at drawings, and there’s lots of trial and error. It raises the transaction cost.
“You need a special relationship with your suppliers to make this work. The Japanese are comfortable with these long-term, trust-based relationships. But U.S. automakers wanted a market relationship, and this leads to dysfunctional interactions. Since 1992, 37 Tier 1 and 2 suppliers have gone bankrupt, and not one of them was Japanese.”
Despite the need for hands-on engineering at home, automotive work continues to surge offshore. Technology centers support manufacturing operations in China and do R&D in India. General Motors, for example, hired 400 researchers in Bangalore within two and a half years. “If you look at their Internet job postings, they are certainly doing sophisticated research. It’s not for the Indian market, but for global markets and the United States,” said Martin Kenney, a professor of Human and Community Development at the University of California, Davis.
In 2005, an Indian multinational, Tata Group, acquired Incat International plc, an engineering contractor headquartered in Novi, Mich., and London, U.K. Tata, a major manufacturer and IT services supplier, has Incat’s experienced engineers interact with automakers at their facilities and coordinate the flow of engineering work to India.
“Some people tried the offshoring model and found they couldn’t make it work,” said Incat’s head of worldwide delivery, Kevin Fisher. “We can help an OEM with specific parts, like closures or trim, or go from design release to digital manufacturing.” He said Incat is close to signing a large engineering contract with a major automaker.
BUMPS ON THE ROAD
Even as multinationals send engineering abroad, some researchers question some of offshoring’s fundamental assumptions. “You would assume that big companies with smart people running them would do a cost-benefit analysis of offshoring,” Lynn said. “It was not always that sophisticated. They would say, ‘An engineer in India costs one-fifth as much as an engineer here, so the more engineers, the more benefit.’ ”
Lynn said, however, that he talked with two IT firms that estimated that it took five offshore workers to do the work of three U.S. employees. Offshoring also carried additional overhead, such as rework due to misunderstandings, additional management for coordination, and the cost of travel (up to $10,000 or more per person per trip).
“One engineering manager at a household products company told me that when they sent a team to China or reworked a project, they assigned the cost to U.S. operations,” Lynn said. “That made U.S. costs look higher and offshore costs lower.” Managers in other companies told similar tales.
Another company was surprised to find its Indian contractor rotating personnel so more employees could gain experience by working for a multinational client. “The U.S. engineers would fly to India, get to know someone, and the quality of work would go up,” Lynn said. “Then the contractor would rotate personnel and they’d have to make another trip. They were spending their money to train their contractor.”
Kenney notes that until the recession, rapid inflation of Indian IT salaries actually caused many European firms to relocate services in Eastern Europe because costs were similar and the location closer. Lynn believes the true cost advantage of offshoring is more like 15 percent rather than the 50 or 80 percent often claimed.
Yet Lynn readily admits that high costs may be short-term issues of an immature business model. As companies gain experience, offshoring costs may fall. For companies that spend tens or hundreds of millions on R&D, the savings are too tantalizing to ignore.
Besides, developing nations have remade themselves before our eyes. China and India graduate armies of engineers. While quality varies, thousands are smart, hard working, and capable. “If you’re paying an engineer $700 per month, you can afford to train him for nine months. After two or three years, he’ll be equally productive as American workers,” said Vivek Wadhwa, an entrepreneur who is currently executive in residence at Duke University.
Wadhwa also said that Indian IT firms have developed effective corporate training programs. “The IT education you get out of Infosys is better than most of our top universities,” he remarked. Meanwhile, U.S. and European universities are rapidly setting up overseas branches to educate students in science, engineering, and medicine.'
'UNSTOPPABLE NOW’
The shift towards offshore engineering is clear in IT, PCs, and telecommunications. Other industries are being pulled offshore to support new factories, adapt products to local markets, and to seek cost advantages. “Globalization is unstoppable now, no matter how much we moan and groan,” Wadhwa said.
Kraemer agreed. He surveyed 400 companies and sees manufacturing pulling engineering offshore. “The more a company outsourced manufacturing, the more it outsourced the physical design and development of its products,” Kraemer said. His analysis finds that this benefits companies, their industries, and their products. But Kraemer added a note of caution: “In the long run, the real research will probably stay here, but everything else is on the table.”
What will happen next? Will multinationals continue to shift engineering to low-cost nations, or will they reach an equilibrium point? Will smaller companies, typically hotbeds of innovation, feel they must also move engineering offshore to keep up, or will they continue to innovate at home? Will engineering’s center of gravity shift to developing nations?
Ralph Gomory, a former vice president of R&D at IBM and past president of the Alfred P. Sloan Foundation, which supports research about science and society, thinks the interests of corporations and their countries have diverged.
“I’ve sat on corporate boards, and every board member believes it is his or her duty to maximize value for shareholders,” he said. “If offshoring is good for profits, then it is their dutyСand they use that
wordСto take those jobs to other countries.”
[Photo: Bangalore, India, has become a global offshoring destination, graduating from fixing Y2K software bugs and converting 2D drawings into 3D CAD files to doing advanced software design and engineering research and development].
The United States, unlike China, Korea, Japan, or many European countries, makes few demands on its corporate citizens, Gomory said. This has enabled U.S. corporations to shift investments overseas. They have grown richer, but are they leaving the nation poorer?
Classical economists defend offshoring by calling on a centuries-old principle called comparative advantage. It states that countries are better off when they trade without restrictions, so each trading partner can specialize in what it does best rather than try to hang onto floundering industries. Eventually, trade settles into an equilibrium that benefits both partners.
In today’s globalized world, that equilibrium changes constantly. “Comparative advantage tells you nothing about whether today’s equilibrium is better than yesterday’s. Today, we’re consuming more value than we create. We’re not balancing our trade gap. Like a rich family that doesn’t work, we’re living off our inheritance,” Gomory said.
No one can predict how the current recession will affect the global model. According to Hira at RIT, “Companies have built up huge engineering capacities overseas. Now, with the recession, there’s overcapacity. So which part of your capacity do you lop off? The high-cost legacy capacity or the part that you just built?”
Hira’s prediction: “These firms will announce large layoffs and blame it on the recession. But the cuts will be unevenly distributed, so what looks like a layoff is really a geographic redistribution of a firm’s workforce.”
The landscape is clearly changing, but the future is far from clear. The United States, for instance, retains substantial engineering strengths. It remains the leader in R&D investment, sophisticated research, and engineering education. Its engineers remain capable, creative, and highly productive. Its students learn critical skills—teamwork, communications, business sense—that can give them an edge in a global economy.
As the economy improves, perhaps Indian and Chinese engineering salaries will soar once again, until costs reach a rough equilibrium. Perhaps multinationals will then assign R&D tasks based on capabilities rather than cost. Or they may pursue even lower-cost engineers, the way they relocated factories to seek cheaper labor. Perhaps innovation will move to other parts of the world. Perhaps it will simply diffuse across national borders, growing everywhere as the global economy expands.
Whatever happens, the world is definitely changing, and the engineering profession with it.